Paint both protect and provide a new aesthetic impression. Paint is applied to many different surfaces (technically called substrates) like structures such as ships, bridges, buildings, vehicles, and oil & gas. The paint on the steel substrate and paint film is the main focus of the present investigation.
Imagine a liquid paint applied on a steel substrate like ship or oil and gas structure. The chemical curing and physical drying of a liquid paint are relatively fast on the surface-air interface as compared to the underneath layers. A skin layer develops as the processes of curing and drying proceed and a number of changes happen in the freshly applied paint. The main changes are; development of cohesive and adhesive forces, decrease in the paint film thickness, increase in modulus (stiffness), glass transition temperature (Tg) and ultimately when a network is formed the volume changes and give rise to an internal stress. The magnitude of the internal stress in the paint film gradually increases and with time reaches its maximum value depending on the degree of cure and the amount of retained solvents. The temperature of the environment along with humidity plays a critical role in defining the Tg and modulus of the paint film that is directly associated with the internal stress. Therefore, it is important to investigate Tg, modulus and internal stress at the same time and at different temperatures.
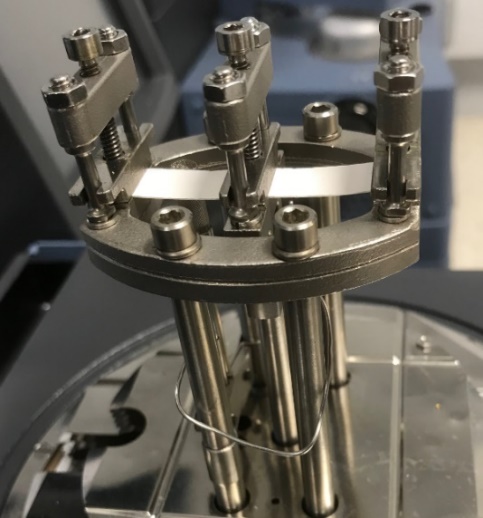
Figure 1) A part of DMA setup
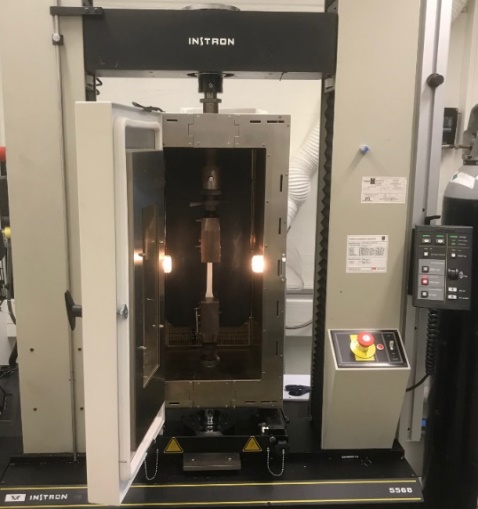
Figure 2) A part of the tensile stress setup
A team headed by Senior Chemist Saif Ullah at Hempel is investigating glass transition temperature (Tg), modulus (stiffness), the coefficient of thermal expansion (CTE) and tensile stress at Aalborg University’s lab facility (Figure 1 and 2) with the help of Professor Jesper de Claville Christiansen and his team. This research work is part of the Fast Track Consortium and funded by Innovation Fund Denmark.
The overall aim of the project is to get a better understanding of what happens in the curing process of the paint film applied on the steel substrate and to develop fast screening methods that will enable us to save development time and produce tough and resilient paint.